by NewsAdmin | Jul 19, 2023 | Jendamark Junction
While there has been a lot of hype around Industry 4.0, the digitalisation of factories has not scaled up as expected. A fundamental misconception of what it’s all about and a slow-to-change mindset are two of the major impediments to successful implementation.
A flood of new products on the market and a misplaced focus on the technologies themselves – rather than their practical uses – leaves many customers overwhelmed, says Jendamark innovations director Yanesh Naidoo.
“There are a lot of buzzwords, like the integration of IT and OT on the shop floor, and I think people get befuddled by all the jargon and consulting talk,” Naidoo says.
“Simply put, Industry 4.0 is just a set of technologies that you can use to solve your manufacturing problems.”
A tech toolbox
It helps to think of Industry 4.0 as a toolbox with a set of tools inside, he explains.
“However, having a toolbox full of tools mean nothing unless you do something with them. You must first understand the problem you’re trying to solve in your factory, and then invest in the right tool for the job.
“A hammer has many uses, but how you apply it depends on your situation. Also, you may be trying to hammer in a screw, when what you really need is a screwdriver.”
For example, if frequent machine breakdowns are a problem, Naidoo says an anomaly detector could help to highlight a downward trend in performance, which could be addressed and fixed before it becomes a serious problem, avoiding unnecessary downtime.
Proactive vs reactive approach
“Essentially, Industry 4.0 is about using tools to be more proactive, rather than reactive. But it all means nothing if our mindset doesn’t change.”
Naidoo draws parallels with the preventative approach to health and longevity outlined in Dr Peter Attia’s book Outlived.
“Medicine 2.0 has been extremely successful in treating lifestyle diseases such as Type 2 diabetes. You go to the doctor, they diagnose you and give you insulin, which has saved many lives.
“But this book argues for a transition to a more preventative approach to medicine. Don’t wait to get diabetes; monitor your health, get the check-ups, make the necessary dietary and lifestyle changes, and prevent it from happening in the first place.”
Factory health screening
Until now, manufacturers have not had the technology or toolbox to take a preventative approach to maintaining the overall health of their factory assets, but Industry 4.0 is changing all that. The difference, Naidoo says, lies in the data that comes from continuous measurement rather than a static, point-in-time measurement.
“A factory audit, like a glucose test for diabetes, is not an accurate reflection of your lived reality,” he says.
“For the glucose test, you fast the night before, then go for the blood test. If your results are just within the acceptable range, everything is deemed fine, so you revert to your bad dietary habits. You’ve prepared your body for the test but that’s not how you live your life, and you can expect future problems if you don’t continuously monitor your glucose levels and make lifestyle changes,” explains Naidoo.
Similarly, he says, a factory audit usually runs quality and production checks using the best operators, the best maintenance team, and the best raw materials on the line.
“It’s a fake perception. What you need is live information from the production line that can be used to understand where the problems are and improve the process by making iterative changes.”
The problem with OEE
With the right technology in place, everything on a production line can be measured continuously – from operator speed to press force and scrap rates. The problem, Naidoo believes, is that every plant manager’s performance is measured on Overall Equipment Effectiveness (OEE), which is a widely used, retrospective, reactive measurement.
“It tells you what happened yesterday, but nothing about what is going to happen tomorrow. Plant managers should be measured on what is going to happen, because they can still have an impact on that.”
Like the human body, all production lines are not the same, so trying to meet a set OEE key performance indicator of, say 85%, might not be practical, given the age of the line, or the quality of the incoming raw material.
“The measurement needs to be unique to a particular production line. As the line gets older, there’s more wear and tear, and breakdowns. So, you need dynamic baseline data that reflects the current situation and can be improved year on year.”
Naidoo says technology can help to predict the risks associated with the people, machine, and product parameters on the shop floor. “Then you can proactively do things to mitigate the risk before it happens.
“We know everyone is under pressure to produce. But at some point, when you see the data trends going in the wrong direction, a manager must have the foresight to make the decision to stop the line and fix the problem, knowing it’s eventually going to hit the limit.
“It’s critical to be proactive because when it hits the limit and things break, you will stop the line. And you will have to make the time and budget to fix it. You’ll have far less downtime if you make adjustments when you notice a spike in anomalies, even if they’re still within tolerance.”
Competitive advantage
Ultimately, Naidoo says, Industry 4.0 is a must for manufacturers who want to remain in business in a rapidly changing environment.
“The world is getting far more competitive. You have to squeeze every single cent you can out of your production process. One of the key things is to become more agile because variation of product, or mass customisation, is now a demand from customers. Your production line needs to be able to adapt quickly and effectively, and also manage fluctuating volumes, without massive capital cost or too much downtime.”
So, what does practical digitalisation look like and where does one start?
If a customer is still hesitant to make changes on the production side, Naidoo says one easy entry point is digitising the maintenance function to facilitate the scheduling of tasks and a more preventative approach to asset health.
“Then once you start seeing the benefits, you can start optimising your assembly process efficiencies by introducing, for example, operator guidance systems. If you choose the right supplier and technology, digitalisation is designed to start small and grow with you step by step, so you get your return on investment.”
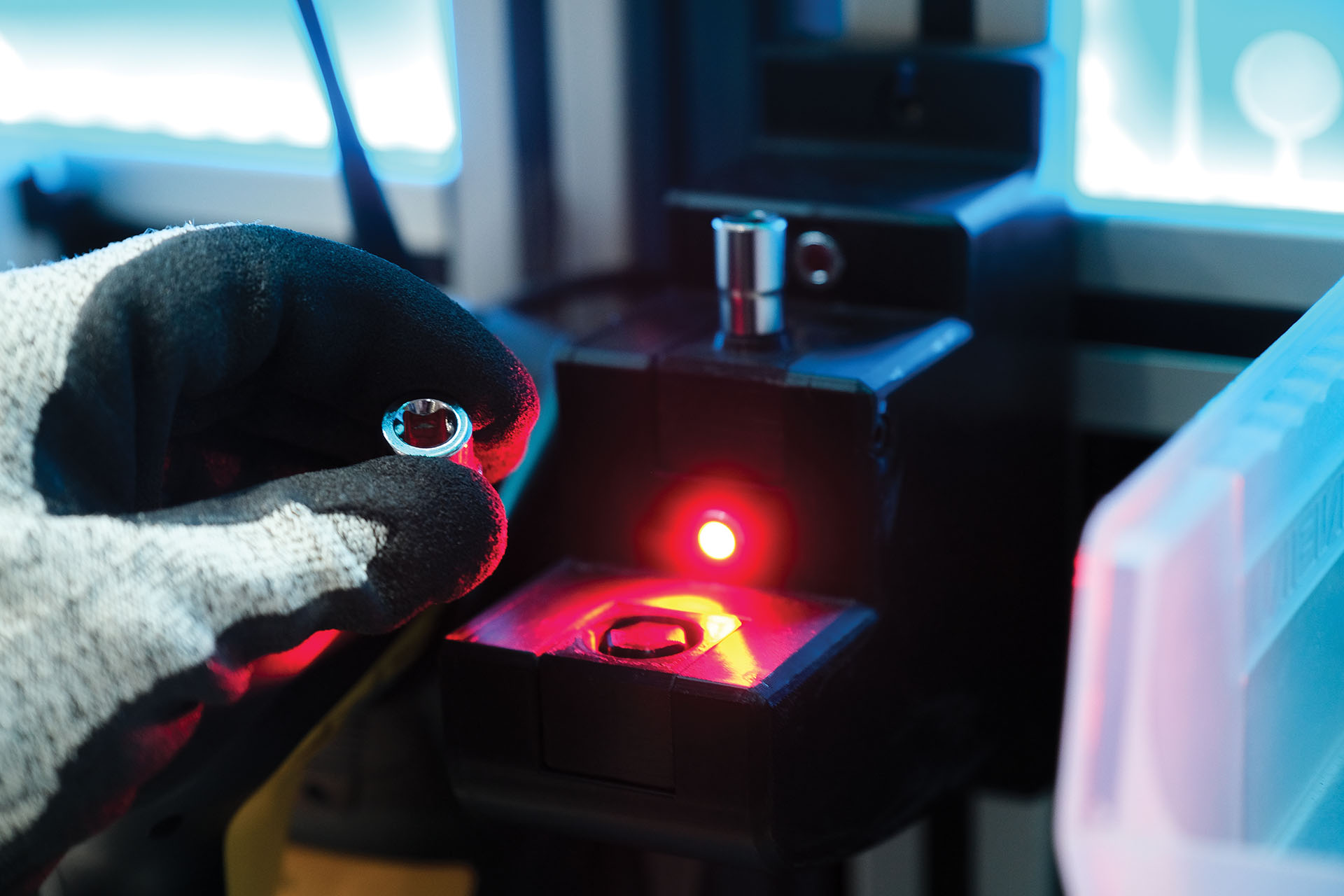
by NewsAdmin | Mar 7, 2023 | Jendamark News
Jendamark India and the Rotary Club of Pune Wisdom have joined hands to connect with corporate clients and help them transform the lives of underprivileged children through our ed-tech tool, ODIN Education.
The educational ecosystem, which was officially launched in India in August, is designed to give every child access to the right digital learning resources, whether they are in cities or remote rural areas.
Even though India has the second largest schooling system in the world, more than a fifth of the population lives below the poverty line and cannot afford to send their children to school. Hence, they do not get the access to education and knowledge that would allow them to compete in the future with their more privileged peers – especially in terms of access to technology.
According to ODIN Education’s business development executive Yogini Bandekar, the signing of the memorandum of understanding with the Rotary Club represents the first major development in getting the system, which is delivered via e-learning tablets, into deserving schools. (Ed: The first roll-out of 50 devices to a rural school near Pune was already under way at the time of writing.)
“We welcome the support of this internationally renowned and trusted community service organisation as we work together to create an educational ecosystem that will empower our children to reimagine a better world,” says Bandekar.
As outlined in the memorandum of understanding (MOU), Rotary will assist in identifying schools in remote areas that need assistance, as well as connecting ODIN Education with clients who can help to put more e-learning devices in children’s hands. Rotary will also arrange the tax benefit certificates for such corporate social investments.
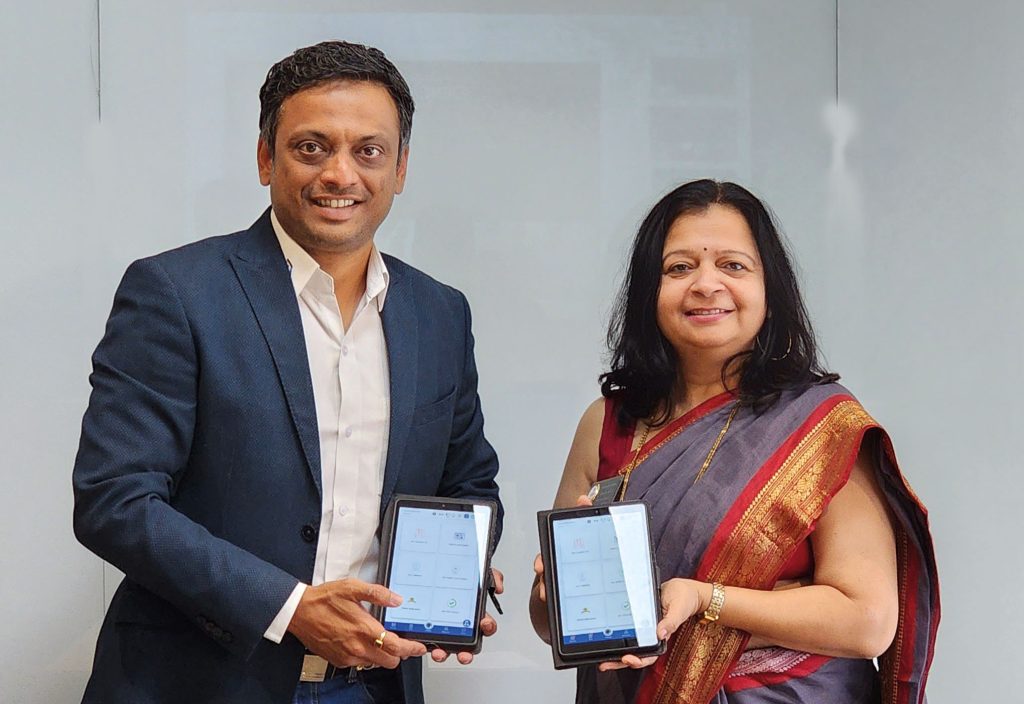
Bandekar says, as part of its corporate social responsibility, Jendamark will handle the practicalities of rolling out the devices, training the students and teachers on how to use them, and sending quarterly reports on engagement analytics to clients to show how their devices are making an impact.
Jendamark India CEO Himanshu Jadhav signed the MOU alongside Rotary Club president Vaishali Varnekar, with past president Hemant Puranik, CSR funding director Nilesh Dhopade and secretary Sarang Balankhe in attendance.
To learn more, contact
info@jendamark.in or visit
www.odineducation.org
by NewsAdmin | Feb 21, 2023 | Jendamark News
An unplanned, last-minute application saw mechanical engineering student Mrudula Joshi beat out a host of other applicants to claim one of two spots in the exciting new international exchange programme initiated by Jendamark India in partnership with MIT-World Peace University.
The 20-year-old Joshi is in her final year of her four-year B.Tech degree but it was her trailblazing involvement in an extracurricular technical club that secured her the two-week trip to South Africa. She is the first female driver for Team Piranha Racing – the university’s official Baja team and Overall Champions at BAJA SAE India in 2021.
The 20-year-old Joshi is in her final year of her four-year B.Tech degree but it was her trailblazing involvement in an extracurricular technical club that secured her the two-week trip to South Africa. She is the first female driver for Team Piranha Racing – the university’s official Baja team and Overall Champions at BAJA SAE India in 2021.
Baja teams design and build their own racing buggies from scratch, with members learning about all aspects of vehicle production from inventory to design, assembly, sales and management.
“My mom always said this is all boys’ stuff. There are no girl drivers. So, from my first year, I wanted to be a driver – that’s the thing I wanted to change,” says Joshi.
“I had no technical experience. During lockdown I learned the software; I always want to learn something new. I worked very hard to move up through the team.”
She says her all-male team has been very supportive and respectful. “They were so happy there was finally a girl. Girls bring emotional intelligence; we keep things neat and orderly. They’re happy about the changes in themselves – it’s a progressive environment.”
Her experience has made her even more determined to pursue a career in vehicle dynamics and testing, and the automotive software behind it.
“It’s true that girls often want to do the software side of things and not get their hands dirty. But if you go into industry, even on the automation side, you need to have basic mechanical skills and an understanding of how things work. An engineer knows how to solve problems.
“I’m doing my internship at an OEM, but I would like to gain experience in a company that is a Tier 1 supplier. That is where all the work happens, whereas the OEM is all about management. You need to have strong technical knowledge before going into management,” explains Joshi.
Through a range of programmes, events and seminars, Jendamark has been instrumental in exposing Joshi and her fellow students to the latest Industry 4.0 technologies, while helping MIT-WPU to develop a curriculum that ensures its students are workplace ready. Joshi’s older brother is one of the students who completed their final-year engineering internship with Jendamark India.
“Other companies are older, but they don’t want to change. Our generation has come with fresh minds. We always want to introduce something new and implement the new things with the existing ones,” smiles Joshi.
“Jendamark in India and South Africa has an amazing culture. The people are friendly, and you can explore opportunities in various departments.
“All aspects of engineering are involved in this automation company. Other companies go for the big things. Jendamark works on a small thing very hard. Right now, they are developing Odin – you could do anything with that software.”
She describes the trip to South Africa, which included visits to Nelson Mandela University’s School of Engineering and School of IT, the world-famous Addo Elephant Park, and, of course, Jendamark Automation’s headquarters, as an amazing experience.
“This is the first time that I’ve travelled without my family. My brother is so proud of me, and they always want to protect me, but now I know what I’m capable of.”
by NewsAdmin | Feb 7, 2023 | Jendamark News
Senior design engineer Reshma Jadhav recently travelled to South Africa where she spent two weeks learning the complexities of catalytic converters before taking up her new role as technical lead for Jendamark India’s canning division.
It has been a rapid rise for Jadhav, who joined Jendamark India just one year ago, after seven years with another automation company.
“At that company, the most complex project that I worked on was a cylinder head cam cover assembly line for a facility in China, which presented a number of challenges, including the cycle times on the line,” says Jadhav.
“Before I joined Jendamark India, I was never exposed to canning projects. So, my initial goal with this intensive training experience in South Africa was to learn all there is to know about the basics, including all tooling and facilities, so that I can impart this knowledge to my team in India.”
Jendamark’s South African team has been developing catalytic converter assembly facilities for almost three decades.
“When I started my training, I was given an induction by Alwyn Smit, who explained the entire design process flow, ensuring that I had a clear foundation. Then each member of the tooling team shared their personal process flow that they follow to ensure that a successful design is released every time,” explains Jadhav.
“I gained exposure to all the various checks that need to be done, the customer data that must be assessed, the tooling calculations that need to be done as well as the lessons learned from these calculations.
“I also learned about parametric modelling when designing multi-body assemblies, which is an incredibly helpful tool that can be used for designing canning tooling.”
Jadhav is excited to share all this newfound knowledge with her team, and see where improvements and increased efficiencies are possible.
She also takes back some fantastic travel memories such as taking time out to experience Gqeberha’s beautiful beaches, seaside flea markets, and game reserves with her colleagues.
“This opportunity is really exciting for me, and I accepted it with open arms. This is a fantastic opportunity for growth, and I will be eternally grateful for all the support and guidance. This new role is a way to develop my career in a well-established company and it’s a great position. I am excited to see what the future holds and looking forward to growing my team around me.”
Jadhav says, as a working mother, the flexibility that Jendamark offers with work-from-home initiatives makes it an adaptive environment that fits in with life’s daily challenges that can arise.
“The fact that Jendamark’s work globally is project-based means that every project we take on is challenging and different. No day is the same and I love coming up with innovative solutions to every one of the various challenges.”