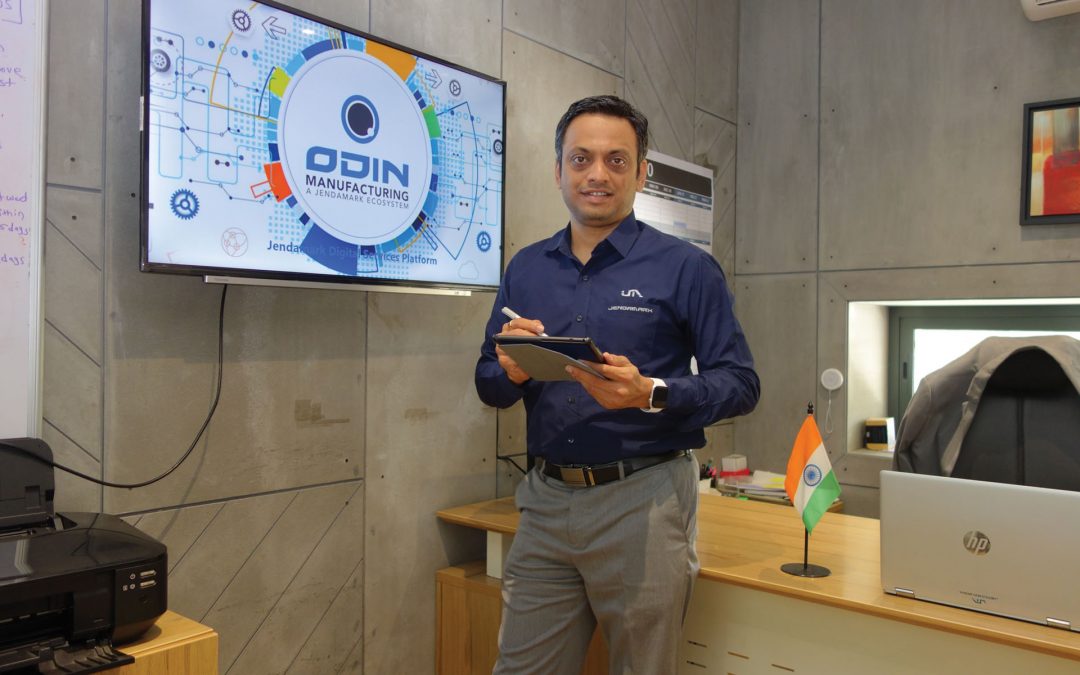
Localisation with digitalisation
Jendamark India CEO Himanshu Jadhav shares his industry expertise in the latest issue of Efficient Manufacturing magazine.
Source: Efficient Manufacturing
Source: Efficient Manufacturing
Jendamark has been offering a virtual design approval process for all customer projects since 2019. A visit to the South African or Indian manufacturing facilities often involves stepping into the fully equipped virtual reality (VR) room for an immersive experience of the customer’s design.
But since the Covid-19 pandemic and subsequent lockdowns made this temporarily impractical, the tech teams turned their minds to the idea of a remote, augmented reality (AR) solution.
“For VR, we had been using Autodesk Inventor with our own content creation,” explains Jendamark India director Himanshu Jadhav. “In mid-April 2020, when Google launched an AR experience to blend digital content into the real world, this got us thinking – and Odin AR was born.”
Jadhav says the objective is to give customers the ability to view their designs in 3D in 1:1 scale, take a closer look at the details and explore different sections from afar.
“The best part of Odin AR is that you don’t need any special hardware or software. All you need is a smart phone with the latest Android or IOS software.
“Our design and tech team create the designs and convert them into AR-ready content. They then generate a link using our cloud service and send it to the customer. All the customer has to do is click on the link and pan across a vacant floor space – and the designs just pop up in front of him or her.”
Jadhav says Odin AR has been available since August, with Dinex, ATS EOL and Tenneco among the first customers to try the technology.
“This will absolutely become part of our standard offering moving forward, and we are working hard to perfect it and create an even more advanced and feature-loaded experience.
“Just imagine a customer being able to use it at the airport, in a hotel room or working from home. Without any special hardware or software, he can view designs, give us valuable feedback and get the 3D immersive experience feel.”
Finland-based Dinex recently commissioned Jendamark India to build canning lines and an after-treatment system assembly line. As their main team is based outside India, AR has become a big advantage. Dinex group engineering manager Kalle Puurula explains why.
Q: With Covid-19 disrupting normal travel and business, how did you experience the virtual 3D design approval process?
A: In these serious times, I have had the great opportunity to get to know and learn the future way for 3D design approval with Odin AR. In the beginning, it was slightly strange that I was looking at 3D models on my mobile instead of playing the same on a laptop with real 3D design software. Sometimes I’m expecting to find the same features as in a 3D design program before I realise that it is not the idea behind this. I have been showing this application to many people and they have been surprised and shown interest in it.
Q: What are the benefits of being able to do virtual 3D design approval?
A: For me, the biggest advantage has been to see the actual size of designed parts. For example, the workstation ergonomic detail has been nice to look through with Odin AR, using a real person in the camera view. The fact that this works on mobile means it’s always available once you get the idea.
Q: Do you see this becoming a normal way of conducting the approvals process in the future?
A: This kind of virtual 3D process will absolutely become more common in future and take on a bigger role in the design approval process. It only takes a few moments to become familiar with it. Good job, Jendamark.
Odin Workstation interacts with the tools, equipment and PLC associated with the line to record and store data, which is used for generating reports on various aspects of production.
Some of the key components of Odin Workstation are:
Odin Workstation is designed to be a user-friendly solution for end users such as operators, line supervisors, production managers and maintenance managers.
Odin Workstation was first implemented on the Audi engine assembly line at the Skoda facility in Aurangabad. With the engine being such a critical component with complex assembly processes, Odin Workstation was able to cater to all the needs of the customer and help them produce quality products.
Operators could build the engine with ease with the help of the worker guidance system by selecting the right parts and tools, and following the defined processes. It led to fewer errors and ensured process poka-yokes (Japanese: ‘mistake-proofing’). Maintenance team could easily find issues that came up during production using the diagnostic tool, thereby reducing overall downtime.
This smart Andon system displays all the data you need as it happens on an easy-to-read dashboard. At the end of each shift, Linewatch sends an email summary of these key parameters:
The main screen shows:
This screen shows:
Please contact the Jendamark India team if you would like to know more.
India’s proposed EV incentive scheme is set to offer significant tax breaks for consumers on the road to achieving a targeted 30% share of all new vehicle sales by 2030.
“Our government is really pushing this issue,” says Jendamark India’s CEO, Himanshu Jadhav. “To achieve this, the government is planning to reduce general sales tax on EVs from 12% to 5%. A few months ago, it was reduced to 12% from 18%.”
Another proposal already implemented is that those buying electric vehicles will receive an additional income tax deduction of Rs 1,50,000 on the interest paid on loans taken to buy electric vehicles.
As a result, he says, buyers are warming to the idea of this new vehicle technology.
“According to a recent survey, 50% of car buyers in India are ready to switch to EVs if the infrastructure is available.”
GOING GREEN
But, incentives aside, the global population in general has a growing awareness of the need to go green.
“Awareness and sensitivity towards climate change and pollution issues is a hidden force for the surge in EV market. Every individual globally wants to reduce his or her carbon footprint,” says Jadhav.
This burgeoning market has seen original equipment manufacturers (OEMs) in India venturing into and ramping up their EV production, which has had a knockon effect for suppliers forced to embrace these new technologies.
Jendamark India has been at the leading edge of these industry developments, designing and building the first battery pack and power electronics assembly line in the country for Mahindra Electric Mobility Ltd.
Power electronics consist of a charger, variable frequency drive and all electrical signal processors which power the vehicle, whereas a power pack is a cluster of batteries put together as a pack which powers the vehicle.
“Battery pack assembly is new technology in India and local equipment manufacturers are not available for EV manufacturers in India, so we have had to depend on European and Chinese equipment suppliers,” Jadhav explains.
“However, Jendamark has invested strongly in the research and development, design and manufacturing of such equipment in India. Our Industry 4.0-enabled assembly lines are helpful in increasing production and lowering the manufacturing cost of battery packs that fit in EVs.”
In fact, battery costs are expected to be cut by half while performance is expected to double over the next decade.
BUILDING BATTERIES
Jendamark’s global head office in South Africa has played an integral role in the design process for Jendamark India’s first EV power pack assembly lines, providing the benefits of its three decades of automotive expertise where needed.
“Following the design phase, we recently built and supplied two assembly lines, both manufactured in India, and are in the process of executing an expansion project for the addition of new variants on the existing lines,” says Shashikant Chaudhari, who was Jendamark India’s management representative on this project.
The human component has also not been overlooked when it comes to technological development.
“Batteries being assembled carry charge. Human safety is very important when you handle charged batteries. Using Jendamark’s own digital manufacturing software, Odin, we monitor and instruct operators in following right assembly sequence to ensure their safety.“
While venturing into new territory has had its challenges, Chaudhari says it has been an exciting journey so far.
“Jendamark is an expert in powertrain solutions for internal combustion vehicles, while EVs have a completely different powertrain. But EVs have brought us tremendous new learning opportunities.”
FACT BOX: CLEARING THE FOG
At the heart of India’s push towards EVs is the government’s all-important clean energy policy aimed at reducing toxic pollution levels.
Jendamark’s virtual reality room allows designers and customers to explore the possibilities of a new production line in three-dimensional reality via an interactive, computergenerated experience.
The introduction of virtual reality (VR) has had tangible, real world benefits for Jendamark customers by enhancing the design review process.
First, the design team makes the complete production line in VR and a member dons the glasses for a walkthrough of the line. This simple step often highlights potential flaws that would not be apparent during a normal design review.
“It’s about seeing the design with fresh eyes,” says Yanesh Naidoo.
“For example, from a maintenance perspective, can the motor be easily replaced or is it stuck underneath in an unreachable back corner? And, as the operator, can one easily reach all the components, and does it really take the time predicted?”
Naidoo says VR is ideal for ironing out any kinks before the design is handed over to manufacturing and for clients to get a better understanding of its workings before sign-off.
“While the line is in production, VR could also be used to train teams of operators on the virtual version, so that they are ready to hit the ground running when commissioning is complete.”